The industrial agitators market is evolving from a stable, utility-driven sector into a dynamic, innovation-led industry. As manufacturers across sectors pursue higher process efficiency, product quality, and sustainability, industrial agitators are gaining renewed strategic importance. No longer viewed as basic mixing components, agitators are being reengineered with advanced designs, digital capabilities, and energy-efficient features to meet changing industrial demands.
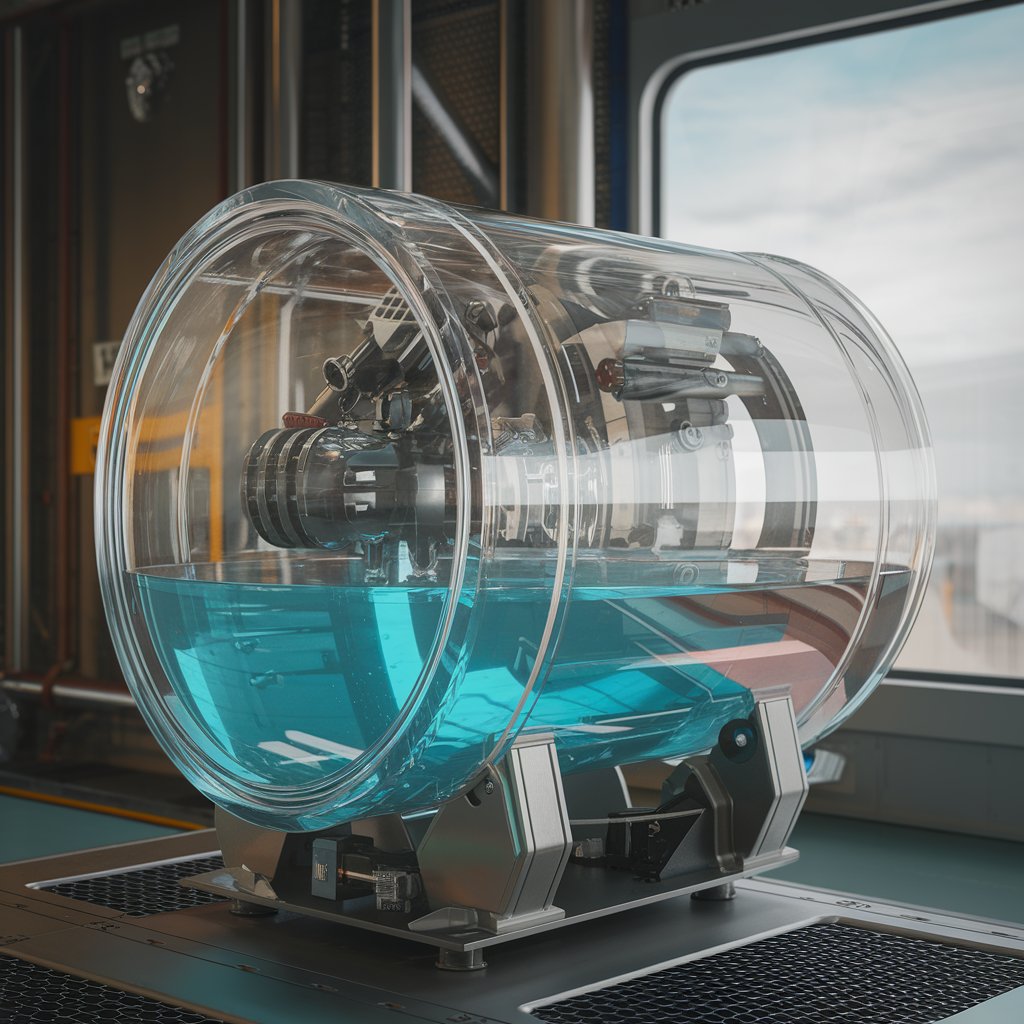
Below, we explore the emerging trends, growth drivers, and technological innovations shaping the future of this market.
Diversified Applications Driving Demand Across Industries
One of the most significant catalysts for growth is the wide applicability of agitators across key process industries. These devices play an essential role in mixing liquids, promoting chemical reactions, dispersing gases, and maintaining homogeneity.
In the chemical and petrochemical sector, agitators are critical in reactors and storage tanks to handle aggressive chemicals and complex compounds. Pharmaceutical manufacturers rely on precision mixing for formulation consistency and to meet stringent GMP (Good Manufacturing Practice) standards. The food and beverage industry uses hygienic agitators for blending, emulsifying, and flavor distribution in high-volume batches, ensuring safety and quality. Meanwhile, water and wastewater treatment plants use agitators for flocculation, neutralization, and sludge treatment—functions that are becoming more important amid growing environmental regulations.
This diverse application base creates a stable and expanding demand across both developed and developing economies.
Technological Innovations Redefining Agitator Design
Recent years have seen significant innovation in agitator design, driven by the need for process efficiency, energy savings, and adaptability. Engineers are moving beyond traditional top-entry or side-entry designs to introduce:
- Customized impeller geometries tailored for specific flow patterns and viscosities
- Magnetic agitators for clean-in-place (CIP) environments and leak-free operation
- Variable Frequency Drives (VFDs) for dynamic control of speed and torque
- Sealless and maintenance-free models for aseptic processes
In addition, smart agitators equipped with sensors, IoT connectivity, and real-time monitoring are gaining popularity. These technologies enable predictive maintenance, fault detection, and data analytics—transforming agitators into intelligent components within smart factory ecosystems.
Download PDF Brochure @ https://www.marketsandmarkets.com/pdfdownloadNew.asp?id=59649096
Sustainability and Energy Efficiency Taking Center Stage
As manufacturers across sectors aim to reduce energy usage and carbon emissions, industrial agitators are being scrutinized for their energy consumption. Traditional mixing systems can be energy-intensive, especially in large reactors or high-viscosity applications.
- To meet sustainability goals, manufacturers are adopting:
- Energy-efficient impeller designs that achieve similar or better results with reduced power input
- Retrofit solutions to upgrade existing agitator systems without full replacement
- Lightweight materials and low-maintenance designs to reduce operational overhead
This focus on sustainability not only improves operational efficiency but also opens up aftermarket opportunities for service providers to help clients modernize legacy systems.
Growth Opportunities in Emerging Economies
Industrial expansion in Asia-Pacific, Latin America, and parts of the Middle East and Africa presents significant growth potential for agitator manufacturers. Rapid industrialization in countries like India, Indonesia, and Vietnam is driving the establishment of new chemical plants, pharmaceutical units, and water treatment facilities—all of which require robust mixing systems.
- Governments in these regions are investing heavily in:
- Urban water and wastewater infrastructure
- Local pharmaceutical and nutraceutical production
- Agrochemical and specialty chemical manufacturing
These developments create a fertile ground for both global players and regional manufacturers to supply localized, cost-effective agitator solutions.
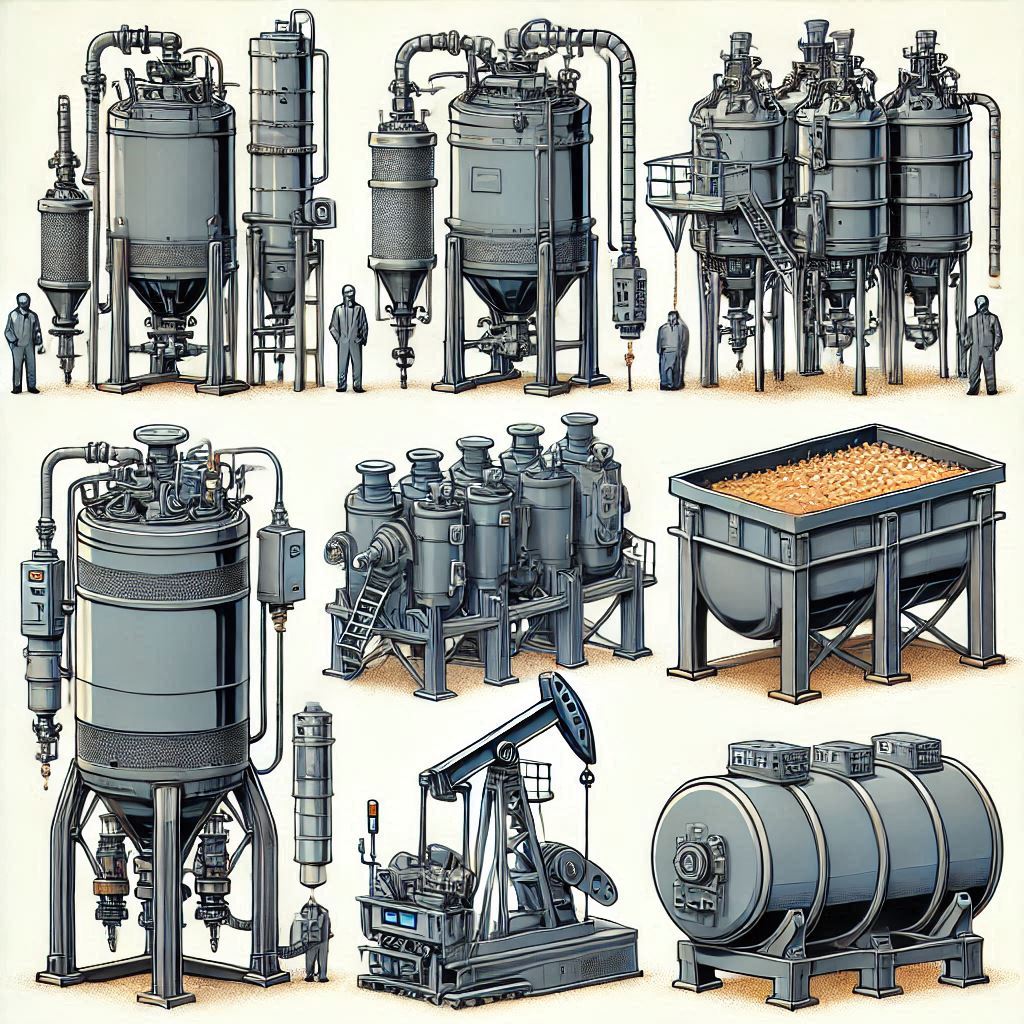
Customization and Application-Specific Engineering
The increasing complexity of industrial processes is pushing manufacturers to move away from standardized products. Instead, there is rising demand for application-specific agitator systems designed to work within unique process conditions—such as tank geometry, product viscosity, reaction time, and contamination risk.
- Industries like biotech, cosmetics, and food processing require:
- Hygienic agitators with electropolished surfaces
- Agitators capable of operating under pressure or vacuum
- Low-shear mixing systems for sensitive ingredients
- This trend favors manufacturers with strong engineering and consulting capabilities, enabling them to provide tailored solutions and strengthen long-term client relationships.
Digitalization and Industry 4.0 Integration
Digital transformation is touching every corner of manufacturing, and industrial agitators are no exception. Smart agitators integrated with sensors and connected to factory automation systems can now:
- Monitor torque, temperature, and vibration
- Alert operators to maintenance needs
- Feed performance data into digital twin models
- Support remote diagnostics and AI-driven optimization
These capabilities enable plant operators to shift from reactive to predictive maintenance, reducing unplanned downtime and improving equipment lifespan.
Market Outlook and Strategic Implications
The Industrial Agitators Industry worth $3.99 billion by 2029, with a CAGR driven by infrastructure development, environmental compliance, and rising product customization. North America and Europe remain mature markets with high-tech adoption, while Asia-Pacific leads in volume growth.
- To capitalize on these opportunities, manufacturers should focus on:
- Design innovation and modularity
- Digital service models and aftermarket support
- Vertical-specific solutions for pharma, food, water, and chemicals
- Global-local strategies to address regional compliance and cost concerns
Conclusion: A Market Ready for Intelligent Growth
The industrial agitators market is undergoing a significant transformation—from simple mechanical mixers to intelligent, efficient, and application-driven systems. With growing attention to sustainability, digitalization, and process optimization, the role of agitators is expanding across industries.
For companies in the sector, the message is clear: invest in innovation, engineering depth, and smart capabilities—because the future of agitation is no longer just about mixing fluids; it’s about enabling smarter, cleaner, and more agile production across the industrial world.