The Industrial Control and Factory Automation (ICFA) industry is undergoing a rapid evolution, driven by digital transformation, supply chain disruptions, sustainability goals, and a skilled labor shortage. At the core of this shift lies a suite of intelligent technologies that are redefining how factories plan, produce, maintain, and adapt.
The industrial control and factory automation market is experiencing robust growth, driven by several key factors. Chief among these are the increasing integration of IoT and AI technologies into industrial environments, a heightened focus on operational efficiency and productivity, and substantial government investments in advanced manufacturing solutions such as 3D printing. As companies adopt emerging technologies, compliance with evolving regulatory standards has become more critical, particularly in ensuring safe and reliable industrial operations. Additionally, there is a growing demand for innovative strategies to minimize production downtime and material waste. For example, the use of real-time data analytics enables factories to monitor and optimize processes dynamically—boosting overall efficiency while significantly reducing waste.
The Global Shift Toward Smart Manufacturing
As global industries aim for greater efficiency, flexibility, and resilience, industrial control and factory automation systems are leading the charge. Technologies such as smart sensors, digital twins, AI-driven robotics, and edge computing are revolutionizing how factories operate, enabling real-time decision-making and predictive capabilities. Regions like North America, Europe, and Asia-Pacific are making significant investments in Industry 4.0 initiatives, aiming to build smarter, more autonomous, and data-driven manufacturing ecosystem
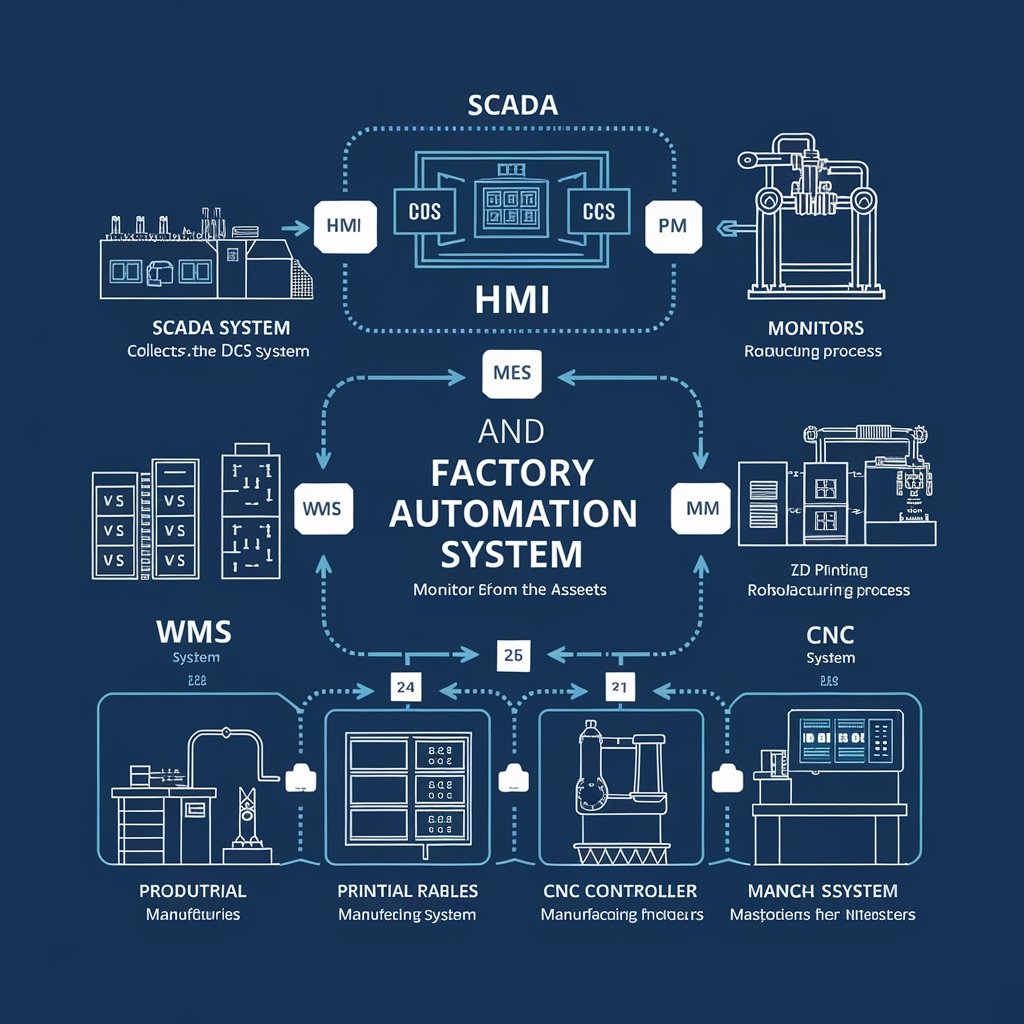
The Rise of Intelligent Systems: Sensors, AI & Edge Computing
The foundation of this transformation lies in smart sensors and Industrial IoT (IIoT). These sensors monitor environmental and machine conditions—like pressure, temperature, and vibration—feeding real-time data to centralized systems for quick analysis and response. Combined with AI and machine learning, this data enables factories to perform predictive maintenance, reduce errors, and optimize processes. Meanwhile, edge computing is empowering these systems to act locally with minimal delay, a crucial advantage for applications like robotics, safety systems, and quality control, where milliseconds can impact outcomes.
Securing the Smart Factory: Cybersecurity and Simulation
With greater connectivity comes greater risk. As IT and OT systems converge, cybersecurity becomes essential to factory operations. Companies are now designing secure-by-default architectures with encrypted data, intrusion detection, and staff cybersecurity training to defend against rising threats. Alongside this, manufacturers are leveraging digital twins—virtual replicas of physical assets—to simulate process changes, test configurations, and optimize workflows. These technologies reduce physical risks, enhance uptime, and streamline innovation in dynamic manufacturing environments.
Future-Proofing with Robotics, Modularity, and AI-Driven Planning
Today’s factories are embracing collaborative robotics (cobots) and robotics-as-a-service (RaaS) models to improve productivity without massive capital expenditure. These robots, guided by AI and vision systems, handle dynamic tasks and ensure worker safety. At the systems level, modular and scalable control architectures are replacing rigid setups, enabling faster reconfiguration and easier integration. Finally, AI-powered supply chain planning is extending the impact of automation beyond the shop floor, helping manufacturers manage inventory, forecast demand, and navigate supply chain volatility with agility and precision.
Download PDF Brochure @ https://www.marketsandmarkets.com/pdfdownloadNew.asp?id=541
Explores the most impactful technologies in the automation ecosystem, offering insights into how each is influencing the modern industrial landscape.
SCADA (Supervisory Control and Data Acquisition)
SCADA remains foundational to industrial automation, offering centralized visibility and control over complex operations. Today’s SCADA systems are evolving with cloud connectivity, edge computing, and IIoT integration, enabling real-time monitoring from anywhere.
New SCADA platforms now incorporate AI for anomaly detection, predictive analytics, and historical data visualization, empowering operators to make faster, more informed decisions. Modern SCADA also supports cyber-secure protocols (like MQTT and OPC UA) to mitigate operational risk in increasingly connected environments.
DCS (Distributed Control Systems)
While similar to SCADA, DCS excels in continuous and process-heavy industries like oil & gas, chemicals, and power generation. DCS technology is now moving toward open architecture, allowing easier integration with third-party analytics tools, digital twins, and advanced process controls.
Key innovations include batch-to-batch learning algorithms, remote configuration, and tighter integration with MES (Manufacturing Execution Systems), enabling holistic plant optimization.
HMI (Human-Machine Interface)
Modern HMI systems are becoming smarter, sleeker, and more intuitive—moving beyond basic displays to touchscreen, voice, and even AR/VR-based interfaces. These improvements empower operators with real-time diagnostics, guided workflows, and mobile access.
Newer HMI software supports HTML5 and cross-platform deployment, making it easier to scale visualization across tablets, control rooms, and remote devices, while enhancing safety and operator efficiency.
MES (Manufacturing Execution Systems)
MES platforms bridge the gap between the enterprise (ERP) and the shop floor. Modern MES solutions are increasingly cloud-based and modular, enabling manufacturers to scale quickly, implement updates remotely, and integrate with other automation layers such as SCADA and DCS.
Today’s MES platforms come equipped with AI-based quality control, dynamic scheduling, and real-time KPI dashboards, allowing greater responsiveness and operational transparency.
PAM (Plant Asset Management)
Plant Asset Management (PAM) systems have transitioned from reactive to predictive. PAM platforms now integrate with IIoT sensors and digital twins to monitor asset health in real time.
With built-in analytics and condition-based alerts, PAM systems reduce downtime, extend equipment life, and optimize maintenance schedules. This is particularly valuable in capital-intensive sectors like mining, pulp & paper, and utilities.
WMS (Warehouse Management Systems)
Warehouse Management Systems are becoming increasingly integrated with AGVs (Automated Guided Vehicles), RFID tracking, and AI-based order picking algorithms. In the age of e-commerce and Just-In-Time delivery, manufacturers are turning to WMS for real-time inventory visibility, predictive replenishment, and labor optimization.
Advanced WMS platforms also sync with ERP and MES to streamline production-to-warehouse handoffs, improving both fulfillment accuracy and delivery speed.
Industrial Robotics
Robots are no longer isolated arms behind cages—they’re becoming collaborative, mobile, and intelligent. Cobots (collaborative robots) now work side by side with humans, handling precision tasks like assembly, inspection, and packaging.
Robotic systems are also increasingly powered by machine vision, force feedback, and AI, enabling dynamic path planning, defect detection, and safe interaction. North American manufacturers are adopting Robotics-as-a-Service (RaaS) to reduce upfront investment and scale automation flexibly.
3D Printing (Additive Manufacturing)
Additive manufacturing is becoming a strategic tool in factory automation industry , especially for rapid prototyping, tooling, and custom low-volume parts. Manufacturers are now integrating 3D printers into their production lines to produce jigs, fixtures, and end-use parts directly at the point of need.
As material range, speed, and precision improve, 3D printing supports on-demand manufacturing, reduces inventory costs, and enhances design innovation.
CNC Controllers
Computer Numerical Control (CNC) controllers are becoming more connected and intelligent. Equipped with real-time monitoring, closed-loop feedback, and AI-based path optimization, next-gen CNCs are driving smarter metalworking, milling, and machining processes.
Modern CNCs also support remote programming, diagnostics, and integration with MES/SCADA systems, improving production speed, reducing material waste, and minimizing downtime.
Process Analyzers
Process analyzers are crucial for quality control in industries like pharmaceuticals, chemicals, and food processing. Recent innovations include inline sensors, spectroscopic analysis, and real-time chemical composition monitoring.
These analyzers provide continuous quality assurance, reduce reliance on lab testing, and support regulatory compliance through accurate process validation.
Flow Meters
Flow meters are no longer just about volume—they now measure viscosity, density, temperature, and pressure, too. With IIoT integration, smart flow meters provide real-time data to SCADA and MES systems, improving process control in water treatment, oil refining, and beverage manufacturing.
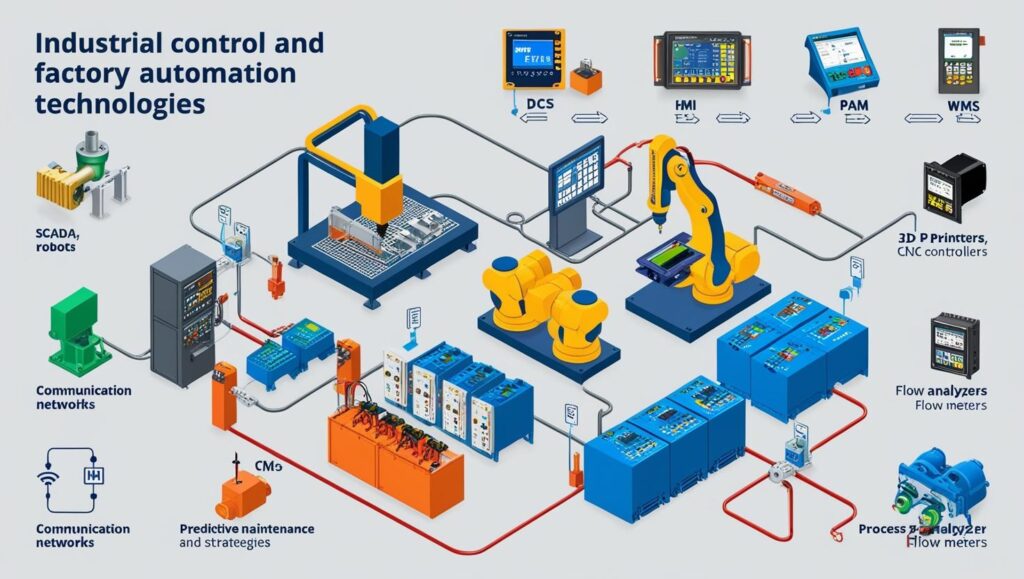
Some models now support self-calibration and predictive failure alerts, reducing maintenance costs and enhancing process reliability.
Industrial Communication Protocols
The rise of digitalization demands robust, standardized communication between devices and systems. Protocols like OPC UA, Profinet, EtherNet/IP, and MQTT are enabling secure, deterministic, and scalable machine-to-machine (M2M) and machine-to-cloud (M2C) communication.
These protocols are essential to interoperability, real-time control, and cloud analytics in smart factories. Many vendors are adopting Time-Sensitive Networking (TSN) to reduce latency and ensure time-critical data delivery.
Predictive Maintenance
Predictive maintenance has evolved from theory to industrial reality. Powered by machine learning, vibration analysis, and thermal imaging, modern systems forecast equipment failure before it happens.
Integrating with MES and PAM, predictive maintenance helps optimize labor planning, spare part inventory, and maintenance workflows—resulting in reduced downtime and operational cost savings of up to 30–40%.
Machine Safety and Compliance
As robots and automated machinery become more integrated with human workers, safety systems are becoming more sophisticated. Technologies such as safety light curtains, area scanners, emergency stops, and interlock systems are being enhanced with AI and sensor fusion.
Safety standards like ISO 13849 and IEC 62061 are pushing manufacturers to implement certified machine safety architectures that combine productivity with compliance.
Final Outlook: A Hyper-Connected, Adaptive Industrial Ecosystem
The industrial control and factory automation space is shifting from hardware-centric systems to data-driven, AI-enabled, and cloud-connected ecosystems. Manufacturers that embrace this technology stack will benefit from faster innovation, better resilience, reduced waste, and smarter human-machine collaboration.
As we approach 2025 and beyond, automation will no longer be a differentiator—it will be a baseline requirement for survival and growth. Those who lead in deploying these technologies will define the next generation of smart, agile, and efficient factories.